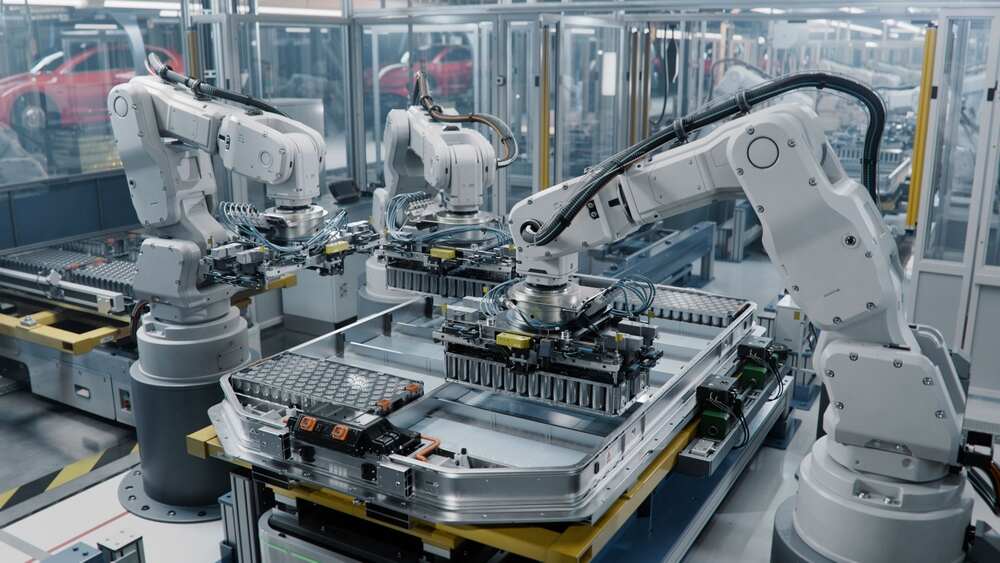
A Manufacturing Execution System (MES) is a powerful tool that helps manufacturers run their production processes smoothly and efficiently. But what is MES exactly, and why is it such a game-changer in today’s manufacturing world? In simple terms, an MES connects, monitors, and controls complex manufacturing processes on the shop floor in real time. It acts as a bridge between Enterprise Resource Planning (ERP) systems and production operations, providing essential insights for better decision-making and production control.
In this guide, we’ll break down how an MES works, why it’s essential for modern manufacturing, and the key benefits it can bring to your business.
What Is MES?
So, what is MES? A Manufacturing Execution System (MES) is a software solution designed to manage and optimize production activities within a manufacturing plant. From planning and scheduling to quality control and production tracking, MES software keeps tabs on everything happening on the shop floor. Think of it as the control tower that guides production operations, ensuring every task and work order is on track.
MES offers manufacturers a real-time overview of their operations, making it easier for decision makers to manage and improve every step of the production process, from raw materials to finished goods. By gathering and analyzing real-time data on production activities, MES enables manufacturers to respond quickly to issues, keep quality in check, and boost productivity.
How Does a Manufacturing Execution System Work?
Wondering how does a manufacturing execution system work? An MES software solution works by capturing real-time information on work orders, production schedules, and other essential details about shop floor operations. It then uses this data to help manage production flow, ensure quality standards, and coordinate with resource planning ERP systems for a seamless production environment.
Here’s a quick rundown of how an MES system typically operates:
- Data Collection: An MES continuously collects data on production tracking, machine performance, overall equipment effectiveness (OEE), and more. This data is then available in real-time for decision-making.
- Monitoring Production: MES software keeps track of every stage in the production process, giving an overview of the status of every work order.
- Managing Quality Control: An MES ensures that quality standards are met throughout the production cycle. It highlights quality issues as they arise, so they can be resolved immediately.
- Improving Production: With insights from MES, manufacturers can identify areas for improvement, fine-tuning processes to optimize efficiency and minimize waste.
MES integrates with other systems, such as ERP solutions, to provide a complete view of business operations, from supply chain logistics to the shop floor.
Why MES Matters for Manufacturers
The value of a Manufacturing Execution System goes beyond simply monitoring production. Here are some key reasons why MES is essential for modern manufacturers:
1. Real-Time Production Tracking
With MES, manufacturers get real-time data on every aspect of production. This enables faster decision-making and reduces delays since teams can spot issues immediately and make adjustments. For instance, if a machine shows signs of downtime, the MES can alert managers to address the issue before it escalates.
2. Quality Management and Control
Maintaining high product quality is crucial for any manufacturer. MES helps enforce quality control by monitoring standards at every stage of production. If a quality issue arises, the MES flags it, allowing the team to resolve it right away. This proactive approach helps prevent defects and ensures that only top-quality products reach customers.
3. Better Production Scheduling and Resource Planning
Effective production scheduling is essential for timely delivery. MES systems coordinate with ERP software to create efficient schedules, maximizing resource planning ERP systems and ensuring that each work order is completed on time. With accurate production schedules, manufacturers can avoid bottlenecks and streamline operations.
4. Improved Overall Equipment Effectiveness (OEE)
Overall Equipment Effectiveness (OEE) is a measure of how well manufacturing equipment performs. By tracking OEE metrics, MES provides insights into equipment uptime, performance, and quality. This information allows manufacturers to improve machine efficiency, reduce downtime, and increase productivity.
Key Benefits of an MES Solution
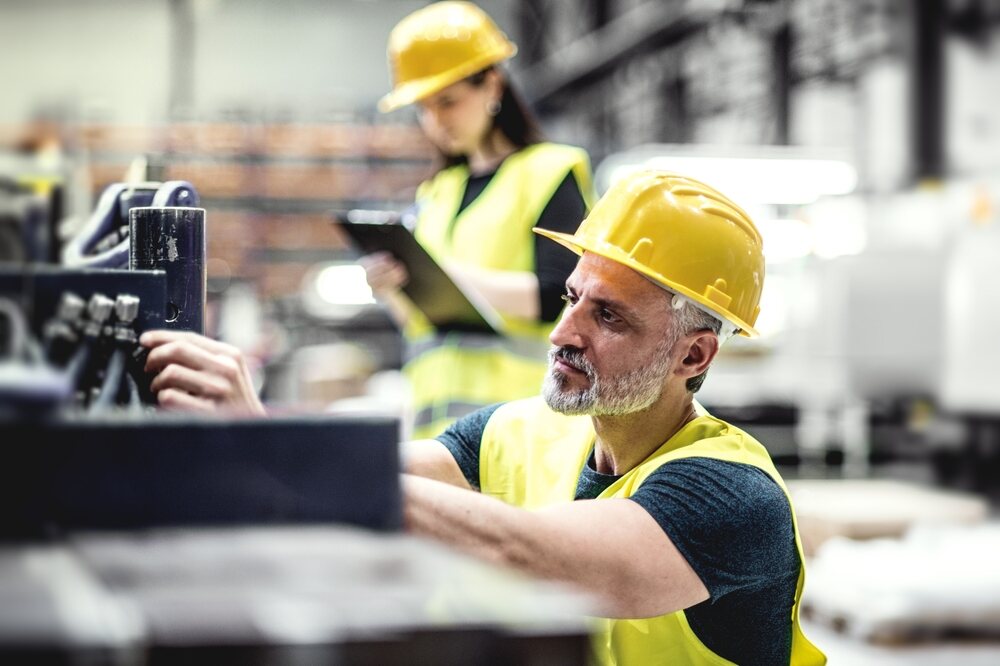
An MES solution offers several advantages, making it an invaluable tool for any manufacturing operation:
- Enhanced Visibility: Real-time access to production data means managers have full visibility into the shop floor. This helps them stay informed and react quickly.
- Reduced Costs: By streamlining processes and preventing waste, MES contributes to cost savings in production.
- Continuous Improvement: With insights from MES, manufacturers can constantly refine their processes to improve productivity and quality.
- Increased Accountability: MES creates an audit trail, so every production activity is tracked, helping with compliance and accountability.
Implementing an MES for Continuous Improvement
Manufacturing is an ongoing process, and an MES supports continuous improvement by highlighting opportunities to optimize production. Through data analysis, it identifies areas where processes can be refined, or resources used more efficiently. Continuous improvement leads to more reliable production schedules, better-quality products, and increased customer satisfaction.
MES and ERP: A Powerful Duo
One of the biggest strengths of an execution system (MES) is its ability to work hand-in-hand with ERP solutions. While ERP systems focus on high-level business functions like accounting, sales, and supply chain management, MES zooms in on production operations. Together, they provide a complete view of the business, from raw materials to finished products.
With the integration of MES and ERP, data flows seamlessly between the shop floor and back-office operations. This integrated approach supports everything from quality management to production tracking, creating a unified and efficient production environment.
Why Real-Time Data Is a Game Changer
In today’s fast-paced manufacturing world, real-time data is invaluable. The MES manufacturing execution system captures data from machines and production lines as it happens, providing insights that can be acted on immediately. Real-time data allows managers to make informed decisions, which can mean the difference between meeting production targets and missing them.
Whether it’s spotting a quality issue or identifying a machine running below capacity, real-time data helps manufacturers stay agile and responsive. In an industry where every minute counts, this instant insight is a competitive advantage.
The Bottom Line
So, why does MES matter? An MES solution is essential for any manufacturer looking to optimize their production activities and achieve high standards in quality control. By providing real-time insights, improving production tracking, and ensuring better use of resources, MES allows manufacturers to reach their full potential on the shop floor.
If your goal is to improve overall equipment effectiveness (OEE), maintain better control over production schedules, and gain visibility into every aspect of your operations, then an MES may be the missing piece you need. An MES doesn’t just track production—it transforms it, creating a streamlined, efficient, and data-driven approach to manufacturing.
Incorporating an MES into your business isn’t just about staying competitive; it’s about setting your business up for success in an increasingly digital, data-driven world. With MES, you’re not just managing production—you’re mastering it.